For wineries aiming to keep on top of barrel storage racking, a forklift with a licensed driver employed on the team is often an essential requirement. However, some suppliers are beginning to think of innovations that could take wine barrel storage in new directions.
Journalist Samuel Squire spoke to one SA-based stackable barrel rack manufacturer to find out more.
The arduous task of moving barrels stored in a winery could be in line for an upgrade â although itâs still early days for one concept with the potential to change conventional racking systems.
Traditional storage methods usually involve holding two barrels per rack, with these stacked vertically, but one innovating product developer says there may be a way to improve this.
A prototype of the concept was unveiled at last yearâs WineEng National Conference and Exhibition in the Barossa, receiving a positive response from those introduced to the new design.
The concept is a simple one: barrels are moved mechanically, removing the need for physical work or the use of larger machinery, such as forklifts, to undertake this task.
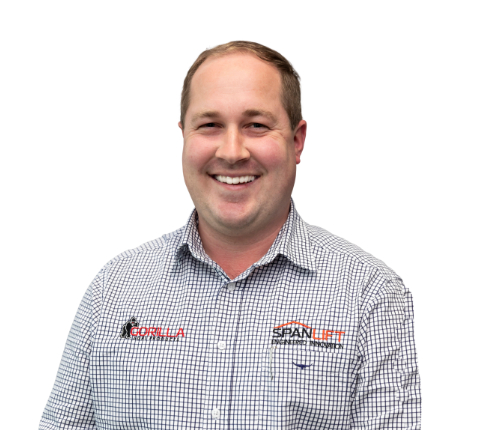
Joe Grace, from Spanlift, has been involved in the manufacturing and supply of barrel stacking solutions for many years under the Gorilla Agri Products brand.
He says while the moving barrel storage system is still in a phase of R&D to deliver a commercial product to market, thereâs scope for it to eventually undergo winery trials.
Grace believes that, if successful, the system could utilise forms of automation, thus potentially offering greater efficiencies as well as a reduction of labour inputs for winemakers going through the process of moving heavy wines-in-barrel.
He said another benefit of a âmachine racking systemâ may be that it could help to make barrel moving safer for winery cellar hands.
âFeasibly, something like this could be [ready] in the next four or five years, and would benefit those that are seeking to move away from the older style racks to newer, safer racking options,â Grace explained.
He said that currently, more consideration is needed to design a way for the system in development to allow racks to be âstacked and unstacked easilyâ.
The greatest challenge for the concept though is finding a way for it accommodate barrels of different sizes.
âMore thought needs to be put in to allow for different-sized racks, to accommodate different sized barrels [so these can] be easily used and [âŠ] recognised by automated systems.â
To enhance the use of the system, Grace says scanning and barcode recognition for identifying barrels and âwhat is stored whereâ could also be utilised.
Until theses advancements arte fully developed, Grace says there are other options available on the market that, while not as technologically ambitious, can provide systems for rotating barrels once these are shelved and stacked.
Although, he acknowledges that there may be safety issues related to these.
Safety concerns
âThe original Falland rack, for example, is easy to use, has been around for many years and fits most barrels,â he said.
âOn this system, the round rod does not cut into the barrel. It is fully hot dip galvanized and lasts forever.
âHowever, it is an older system and is not as safe. It relies on the integrity of the barrel for stability.
âYou have to put similar barrels on each rack (two per rack) to make it easy to stack and you can only stack barrels five-high.
âStacks tend to be very wobbly and require experienced cellar hands to stack.â
Grace says one option to eliminate issues surrounding OH&S is another product, the patented âBarrel Masterâ, which includes optional castor wheels to make it easier to turn barrels for cleaning.
âItâs a rack-on-rack system which removes safety issues, including relying on the structural integrity of the barrels for support.
âIt also features a patented locating system which allows for easy stacking â suitable for the less experienced forklift operator to stack.â
He says that this system, while not machine operated or autonomous, removes the chance of kicking your shins on sticking-out rack feet.
âThere are no feet sticking out to get caught on anything, itâs very stable and can stack up to eight high safely,â he said.
This article was originally published in the September issue of The Australian & New Zealand Grapegrower & Winemaker. To find out more about our monthly magazine, or to subscribe, click here!
To view the current issue of the Grapegrower & Winemaker, visit our Current Issue page.
Are you a Daily Wine News subscriber? If not, click here to join our mailing list. Itâs free!